This website uses cookies. By using this site, you consent to the use of cookies. For more information, please take a look at our
Privacy Policy.
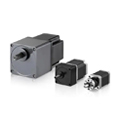
Encoders
An encoder is an electrical mechanical device that converts linear or rotary displacement into digital or pulse signals. The most popular type of encoder is the optical encoder, which consists of a rotating disk, a light source, and a photo detector (light sensor). Encoders are used to translate rotary or linear motion into a digital signal. Usually this is for the purpose of monitoring or controlling motion parameters such as speed, rate, direction, distance or position.
Types of Electromechanical
Picture & Models
Description
RoHS
Datasheet
Lifecycle Status
Quantity
Operation
FAQ
- What is an Encoder?
- An encoder is an electronic device used to convert mechanical motion into an electrical signal. It provides feedback on the position, speed, and direction of a rotating or linear object.
- What are the main types of Encoders?
- Rotary Encoders: Used to measure the rotation of a shaft or object. They provide information about angular position, speed, and direction. Linear Encoders: Measure linear displacement or motion along a straight path. They provide position and velocity data.
- What are the main applications of Encoders?
- Robotics: Controlling joint angles and end effector positions. CNC Machines: Positioning and controlling tool movements. Motor Control: Feedback for speed and position control. Conveyor Systems: Monitoring and controlling product movement. Automotive: Steering angle measurement and wheel speed sensing. Aerospace: Flight control systems and navigation.
- How do I choose the right Encoder for my application?
- Consider factors like the type of motion (rotary or linear), required resolution, accuracy, environmental conditions, output type (analog or digital), and interface compatibility. Consult datasheets and manufacturer resources for guidance.